Les procédés de fabrication soustractive, par exemple, le fraisage ou le tournage, consiste à enlever de la matière jusqu’à ce qu’il ne reste que la géométrie de la pièce. À l’inverse, les procédés additifs, également connus sous le nom de fabrication additive ou d’impression 3D, construisent des composants en métal, en plastique, en céramique, en verre, en sable ou d’autres matériaux couche par couche jusqu’à ce qu’ils atteignent leur forme finale. Les composants complexes peuvent être fabriqués à proximité du contour final en une seule étape du processus.
De nombreux composants métalliques imprimés en 3D nécessitent, notamment lorsque des exigences élevées sont imposées aux propriétés mécaniques telles que la résistance et la ténacité, un traitement thermique adéquat au terme du processus de fabrication.
La nécessité d’un traitement thermique des composants fabriqués de manière additive peut être motivée par des raisons très diverses. Tout d’abord, il faut se rappeler que ces composants présentent de nombreuses caractéristiques qui diffèrent de celles des composants moulés, forgés ou usinés, lesquels ne représentent souvent pas l’état optimal pour une utilisation immédiatement opérationnelle :
- Les composants produits par fabrication additive présentent souvent des pores ou des fissures causés par une fusion incomplète de la poudre ou par un manque d’homogénéité dans le refroidissement du métal.
- Les composants fabriqués selon la méthode additive présentent des distributions granulométriques localement différentes en raison de l’histoire thermique. Du fait de la solidification, les grains présentent une mutation préférentielle claire dans la direction verticale.
- En outre, dans la plupart des cas, la microstructure directionnelle conduit à des propriétés mécaniques dépendantes de la direction (anisotropie). Dès lors, la résistance statique et dynamique, ainsi que la ténacité d’un composant fabriqué de manière additive, peuvent présenter des différences significatives entre les directions transversale et longitudinale.
- La fabrication additive se caractérise par un apport d’énergie thermique localisé, un refroidissement rapide et la répétition du procédé à chaque dépôt d’une nouvelle couche sur la pièce. Il en résulte inévitablement des contraintes locales de compression et de traction, qui se traduisent par un état complexe de contraintes résiduelles du composant au terme du processus de fabrication.
Dans la plupart des cas, les caractéristiques précitées ont un effet négatif sur la capacité de charge des composants fabriqués de manière additive, ce qui restreint les possibilités d’utilisation de ces derniers dans les applications à forte sollicitation. En revanche, un traitement thermique optimisé permet d’éliminer ou de réduire un grand nombre des inconvénients liés à la production, et améliorer ainsi considérablement les propriétés mécaniques. Ainsi, le traitement thermique dans la chaîne de processus de fabrication additive constitue un enjeu essentiel.
En fonction des besoins, les traitements suivants peuvent être appliqués à la chaîne du processus de fabrication additive :
Avant le processus de fabrication | Dessiccation de la poudre |
---|---|
Après le processus de fabrication | Déliantage Frittage Recuit de détente Recuit normal Recuit de diffusion Pressage isostatique à chaud (HIP) Procédés thermochimiques de traitement thermique |
La dessiccation est l’un des processus réalisés en amont. La qualité constante des composants exige une qualité élevée et constante de la poudre.
Durant l’entreposage, il arrive que la poudre absorbe de l’humidité, ce qui peut entraîner des pertes de qualité dans le composant fabriqué. La dessiccation à des températures modérées permet de contrer ce phénomène.
Déliantage et frittage
Dans les procédés de fabrication contenant un liant, la poudre est combinée à un agent liant (généralement sous forme de résines) lors de la première étape de la fabrication du composant, puis ce mélange est appliqué en couches. Le résultat est un composant suffisamment résistant pour permettre le transport interne. Les agents liants doivent généralement être expulsés du composant avant le processus de frittage.
Le déliantage s’effectue en échauffant le composant à la température d’évaporation du liant. Cette température doit être maintenue très précisément de sorte que les produits de décomposition gazeux puissent se diffuser hors du composant. Pendant, et surtout après l’élimination du liant, le composant est extrêmement instable, car il n’existe pas de liaison solide entre les différentes particules. C’est pourquoi, après le déliantage, le composant est stabilisé par frittage, ce qui lui confère la résistance requise.
Le déliantage et le frittage nécessitent chacun des températures spécifiques selon le processus. L’utilisation d’étuves combinées couvrant les deux plages de température évite le transport entre les étapes de travail.
Le déliantage et le frittage des composants métalliques sont généralement effectués en présence de gaz inertes qui protègent les composants de l’oxydation. L’utilisation de gaz inertes contenant de l’hydrogène est également possible.
L’emploi d’hydrogène, ainsi que les vapeurs produites lors du déliantage, nécessitent un système de sécurité adapté à l’installation de l’étuve.
Gaz utilisés :
Approvisionnement en gaz :
Recuit de détente
Les contraintes résiduelles élevées que présentent la plupart des composants fabriqués de manière additive représentent un risque élevé de fissuration, ainsi qu’un potentiel élevé de déformation. On applique par conséquent un recuit de détente sur presque tous les composants métalliques à titre de première étape postérieure à la fabrication additive.
La dégradation thermique des contraintes résiduelles est initialement due à la diminution de la résistance du matériau liée à l’augmentation de la température. Les contraintes résiduelles qui dépassent la limite d’élasticité en fonction de la température sont dégradées plastiquement. Étant donné que les déformations plastiques qui en résultent peuvent entraîner des modifications de dimensions et de forme, il est recommandé de laisser les composants non séparés sur la plateforme des composants pendant le recuit de détente. Les composants sont ainsi plus stables.
Afin d’éviter l’oxydation de la surface métallique, le recuit de détente doit être réalisé sous atmosphère protégée.
Gaz utilisés :
Approvisionnement en gaz :
Recuit de normalisation et de diffusion
En raison de l’orientation préférentielle de la microstructure, les propriétés mécaniques des composants fabriqués de manière additive sont souvent anisotropes.
Pour assurer l’homogénéisation de la microstructure (établissement d’une forme et d’une taille de grain uniformes) et des propriétés mécaniques (élimination de l’anisotropie), un recuit de normalisation ou de diffusion sous atmosphère gazeuse définie peut être appliqué aux composants métalliques fabriqués par méthode additive.
Gaz utilisés :
Approvisionnement en gaz :
Pressage isostatique à chaud (HIP)

Le pressage isostatique à chaud (HIP) élimine la microporosité des composants fabriqués par méthode additive. La combinaison de valeurs très élevées de pression (jusqu’à 3 000 bar) et de température (jusqu’à 2 000 °C) élimine la porosité interne par déformation plastique, fluage et diffusion.
En réduisant la porosité interne par pressage isostatique à chaud, il est possible d’atteindre jusqu’à 100 % de la densité théorique. Dans le même temps, la ductilité est accrue et la résistance à la fatigue se trouve considérablement améliorée.
Gaz utilisés :
Approvisionnement en gaz :
Procédés thermochimiques de traitement thermique
Afin d’obtenir une résistance maximale des composants fabriqués par méthode additive, des processus thermochimiques (tels que la cémentation, la carbonitruration ou la nitruration) peuvent être réalisés lors de l’étape finale du processus, en fonction de la composition du matériau.
Les procédés de traitement thermochimique des composants fabriqués par méthode additive sont soumis aux conditions suivantes :
- Les composants ne doivent pas être trop complexes, filigranes, à parois fines, asymétriques ni rugueux.
- La surface doit être active (exempte d’oxydes ou d’autres couches de passivation).
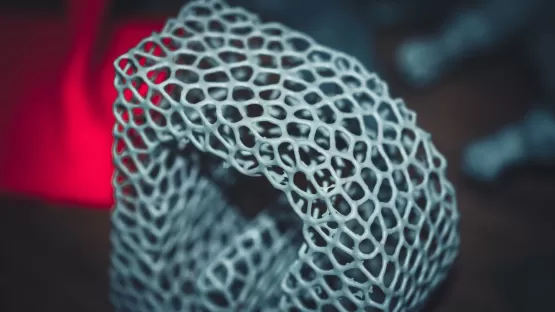
Les structures complexes et à parois minces présentent des défis particuliers en termes de traitement thermique. Dans le cas de ces structures, le traitement thermochimique est associé au risque de cémentation ou d’adhésion complète, qui peut entraîner un effet négatif sur les propriétés mécaniques. En outre, les structures fines et complexes sont très sensibles aux déformations, notamment lors de la trempe.
Les milieux de trempe liquides (huiles, sels) peuvent contaminer fortement les structures internes, ce qui pose des difficultés lors du nettoyage ultérieur des composants. C’est pourquoi des gaz sont souvent employés comme agents de trempe dans les structures complexes. L’utilisation de la trempe sous gaz à haute pression permet de réduire considérablement les fluctuations de dimension et de forme et d’éliminer complètement le nettoyage ultérieur de la chaîne de traitement.