- Découpage au laser économique : adopté dans de nombreux secteurs industriels
- Comment fonctionne le découpage au laser ?
- Gaz de résonance pour laser CO2 : qualité élevée et longue durée de vie lors du découpage au laser
- Accessoires propres aux systèmes d’alimentation en gaz pour la mise en œuvre des gaz de résonance dans le cas du découpage au laser
- Gaz de process pour le découpage au laser : la technologie laser dans le domaine de la fabrication - Les différents procédés
- Quels sont les procédés utilisés pour le découpage au laser ?
- Différents gaz de process pour le découpage au laser
- Découpage au laser efficace avec la buse LASAL Touch : plus de puissance, moins de consommation de gaz de process
Découpage au laser économique : adopté dans de nombreux secteurs industriels
Le découpage au laser est un procédé qui consiste à couper des corps solides au moyen d’un rayonnement laser continu ou pulsé par ablation de matière (enlèvement de matière par chauffage).
Selon l'état de la technique, le découpage au laser convient à pratiquement tout type de matériau, dès lors que les paramètres du rayonnement laser
- longueur d’onde
- puissance moyenne
- énergie et durée de l’impulsion
sont adaptés au matériau.
Les lasers les plus souvent utilisés sont les suivants : laser à haute puissance focalisé, généralement le laser CO2 (laser à gaz), laser Nd:YAG (laser à solide) de plus en plus fréquemment et laser à fibre, plus efficace et facilement focalisable.
Comment fonctionne le découpage au laser ?
La première étape de la production d’un rayonnement laser consiste à exciter un milieu laser par un apport d’énergie (processus appelé « pompage »). Le milieu laser peut être constitué de matériaux très divers. Il est possible d’utiliser des solides (comme un cristal de rubis), des semiconducteurs, des fluides (comme des colorants dissous) ou encore des gaz (comme un mélange d’hélium et de néon).
L’apport d’énergie d’excitation peut être assuré par des lampes flash, des décharges électriques de gaz, des réactions chimiques ou un autre laser.
Pour amplifier le rayonnement, il convient généralement de laisser le processus se dérouler dans un résonateur. Dans ce cas, le rayonnement est réfléchi à chaque extrémité d’un tube par des miroirs et traverse ainsi plusieurs fois le milieu laser.
Gaz de résonance pour laser CO2 : qualité élevée et longue durée de vie lors du découpage au laser
Que ce soit pour les lasers CO2, les lasers à excimère ou les installations spéciales, Carbagas propose le gaz qui convient à chaque résonateur laser. Les gaz et les mélanges de gaz LASALTM sont les garants de la fiabilité de la source laser et allongent la durée de vie des équipements optiques, des miroirs et des lentilles.
Le choix et la qualité des gaz de résonance affectent la stabilité et l'optimisation de la puissance disponible du laser, déterminant ainsi la fiabilité de la source laser.
Pour répondre aux exigences de qualité les plus élevées, les gaz LASALTM présentent les plus faibles impuretés, comme l’humidité, les hydrocarbures et les particules solides. Suivant l’évolution des sources laser, la gamme des produits LASALTM est, elle aussi, étendue et améliorée en continu.
La qualité LASAL
- 100 % d’homogénéité
- H2O < 3 ppm
- Hydrocarbures < 1 ppm
Dans la pratique, il en ressort les avantages suivants :
- Puissance élevée et stabilité du faisceau laser grâce aux faibles teneurs en H2O et hydrocarbures.
- Prévention des problèmes causés par le gaz, comme :
- endommagement du système optique
- variations de puissance
- interruptions inutiles
- entretiens non planifiés
Différents gaz de résonance sont disponibles, dont les qualités et les compositions sont adaptées à diverses installations laser et à leurs spécifications.
Gaz appropriés
Accessoires propres aux systèmes d’alimentation en gaz pour la mise en œuvre des gaz de résonance dans le cas du découpage au laser
Afin de garantir les niveaux de pureté requis jusqu’à l’installation, des équipements spécialement conçus pour les applications laser sont mis à votre disposition pour les robinets.
Des prétraitements complexes des récipients, ainsi que l’homogénéisation des produits et leurs contrôles permanents permettent de garantir que les gaz LASALTM dépassent les exigences de qualité des fabricants de lasers. Ce niveau élevé d’exigences s’applique également à l’équipement et notamment aux systèmes d’alimentation en gaz.
La robinetterie LASALTM offre une alimentation continue en gaz de résonance adaptée aux besoins individuels, du détendeur à double détente à la station de détente pour cylindres et cadres, avec commutation automatique et surveillance électronique du niveau de remplissage.
Gaz de process pour le découpage au laser : la technologie laser dans le domaine de la fabrication - Les différents procédés
Dans le domaine du traitement des matériaux, les appareils laser sont utilisés pour le découpage, la gravure, le perçage et le marquage d’un large éventail de matériaux.
Les avantages de l’usinage des métaux avec un laser découlent des propriétés des faisceaux laser :
- Densité d’énergie élevée, zone thermiquement affectée et charge thermique réduites (déformation minimale)
- Vitesse de procédé élevée
- Usinage sans contact
- Absence d’inertie
- Possibilité d’usiner des matériaux non conducteurs
- Absence d’usure des outils
- Flexibilité importante et bonne automatisation
Quels sont les procédés utilisés pour le découpage au laser ?
En fonction de la température atteinte et du gaz de process utilisé, le matériau enlevé présente différents états d’agrégation. Il convient de distinguer trois variantes, selon que le matériau est retiré de la saignée sous forme de liquide, de produit d’oxydation ou de vapeur :
Découpage au laser par fusion
Lors du découpage par fusion, la formation de la saignée s’effectue par fusion et soufflage en continu du matériau de coupe avec des gaz inertes, le jet de gaz empêchant par ailleurs l’oxydation de la surface. On utilise dans ce cas de l’azote, plus rarement de l’argon ou de l’hélium avec des pressions pouvant atteindre 22 bar.
Une qualité de coupe élevée se caractérise par une faible formation de stries sur les bords de coupe et l’absence de bavures sur la face inférieure de la coupe. La qualité de coupe est influencée de manière déterminante par la position du foyer, la vitesse d’avance, la puissance du laser, la répartition de l’intensité et la pression du gaz de coupe.
Le découpage au laser par fusion est le plus souvent utilisé lorsqu’il est nécessaire d’obtenir des saignées sans oxyde pour les aciers inoxydables. Les alliages d’aluminium et les alliages non ferreux à haut point de fusion représentent un autre type d’application. L’acier de construction normal est également découpé à l’azote, car les bords de coupe n’ont alors plus besoin d’être réusinés en vue de l’application ultérieure d’une peinture ou d’un revêtement en poudre.
Oxycoupage au laser
L’oxycoupage était autrefois le procédé le plus fréquent pour découper les métaux ferreux. Comme dans le cas de l’oxycoupage autogène, le matériau est chauffé à la température d’allumage et brûlé par l’ajout d’oxygène (gaz de soufflage) à une pression de quelques bars. Par conséquent, seuls les matériaux dont la température d’allumage est inférieure à la température de fusion peuvent être usinés.
La largeur de la fente de coupe est comprise entre 0,1 et 0,8 mm environ selon l’épaisseur de la tôle. Il est possible d’éviter quasiment toute formation de bavures lors de l’oxycoupage au laser grâce à la définition de paramètres de procédé appropriés. Afin d’éviter de brûler des contours pointus, ainsi que de former de petits trous irréguliers, la puissance du laser doit être réduite.
Découpage au laser par sublimation
Le gaz de process expulse la vapeur hors de la saignée et empêche également sa condensation à l’intérieur. Les coupes par sublimation sont en principe sans bavures, mais les gaz produits par ce procédé sont souvent inflammables.
Les matériaux ne présentant aucun état de fusion prononcé sont les principales cibles du découpage par sublimation. Il peut s’agir de substances aussi bien inorganiques qu’organiques.
Différents gaz de process pour le découpage au laser
Pour obtenir un bon résultat de coupe sans avoir à retoucher les pièces découpées, la qualité du gaz de coupe joue un rôle déterminant, tout comme le réglage approprié de la focalisation et de la position focale du faisceau laser.
Dans le cas de l’oxycoupage, le foyer du rayon laser est positionné dans le tiers supérieur de l’épaisseur de la tôle. Nous utilisons principalement le gaz LASALTM 2003 en tant que gaz de coupe. Dans le cas du découpage par fusion à haute pression d’aciers fortement alliés et d’aluminium, le foyer est positionné dans le tiers inférieur de l’épaisseur de la tôle. Le gaz de coupe LASALTM 2001 est ici le premier choix. Pour les matériaux particulièrement « réactifs » comme le titane, le gaz de coupe ARCALTM Prime a déjà fait ses preuves.
Application |
Matériaux coupables |
Gaz de coupe |
Oxycoupage au laser |
aciers non alliés et faiblement alliés |
LASAL 2003 |
Découpage au laser par fusion | Acier CrNi métaux non ferreux (Al, Ti) Verre, matières plastiques |
LASAL 2001 ARCAL Prime |
Découpage au laser par sublimation | matières plastiques, papier, Bois, céramique |
LASAL 2001 ARCAL Prime LASAL 4 |
Découpage au laser efficace avec la buse LASAL Touch : plus de puissance, moins de consommation de gaz de process
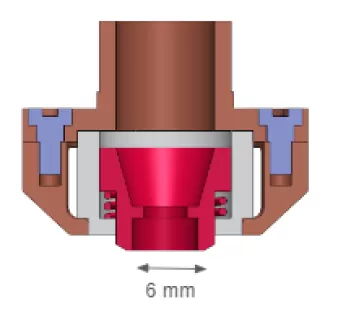
Une buse de gaz permet d’introduire un flux de gaz de process de manière coaxiale au faisceau laser. Ce flux de gaz souffle le métal en fusion afin de l’extraire de la saignée tout en empêchant l’oxydation de la buse de gaz et du matériau à couper.
En raison de la distance entre la surface d’usinage et la buse, une partie du flux de gaz s’échappe latéralement entre la buse de gaz et le matériau. Par conséquent, jusqu’à 90 % du gaz ne contribuent pas à l’éjection du métal en fusion. Pour compenser ce phénomène et obtenir des bords de coupe propres, il est nécessaire de générer des flux de gaz à des pressions élevées, entre 13 et 20 bar, et des débits importants jusqu’à 40 m3/h.
Sur les buses développées par Carbagas, la distance entre la buse de gaz et la surface du matériau est réduite au minimum.
Il y a donc très peu d’espace entre la buse de gaz et la plaque. La quasi-totalité du gaz de process est injectée dans la fente de coupe et ne se perd pas sur les côtés. Environ 90 % du gaz est utilisé « efficacement » pour le découpage au laser.
Buse LASAL Touch : minimisation des coûts liés aux procédés
La buse LASAL Touch permet de réduire considérablement la consommation de gaz de process lors du découpage au laser.
La buse LASAL Touch a été conçue de façon à ne pas nuire à la résistance à la chaleur et à la compatibilité. En cas de changement de production, finis les temps de préparation et donc d’arrêt du laser. Avantages de l’utilisation de la buse LASAL Touch :
- Bords de coupe très lisses et homogènes
- Oxydation minimale au niveau de l’arête inférieure
- Formation minimale de bavures, même dans les angles pointus
- Temps de préparation limités en cas de changement de production
- Augmentation de la vitesse de coupe
- Durée de vie très similaire à celle des buses standard
Vous souhaitez tester la buse LASAL Touch ? N’hésitez pas à nous contacter ! Nous vous soumettrons très volontiers une offre appropriée.